Защита от коррозии металлических и железобетонных конструкций мостов
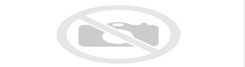
За последние десятилетия в транспортном строительстве использование стальных конструкций стало преимущественным, при этом сохраняется использование несущих железобетонных колонн и железобетонные автомобильные мосты. Современные технологии производства конструкционных сталей, железобетона, новые решения в проектировании транспортных сооружений (мостов, барьерных ограждений, вспомогательных конструкций и сооружений) позволяют устанавливать сроки их службы в десятки лет – 40 … 100 лет. Поэтому вопросы использования качественных защитных покрытий и своевременных ремонтно-восстановительных работ является предметом постоянного обсуждения в данной отрасли.
1. Коррозия стальных конструкций
Прежде чем обратиться к разным видам коррозии, которые проявляются на транспортных сооружениях, в частности, мостовых конструкциях и на барьерных ограждениях дорог, остановимся кратко на описании собственно процесса коррозии.
Коррозия – это электрохимический процесс, который протекает многостадийно. Первоначальная активность проявляется на анодных участках поверхности, где ионы железа (Fe++) переходят в раствор. Высвобождающиеся электроны переходят через металлическую решетку на катодные участки поверхности, где они взаимодействуют с молекулами кислорода и воды, образуя гидроксид-ионы. Эти ионы реагируют с ионами железа, образуя гидроксид железа, который далее взаимодействует с кислородом воздуха и образует гидратированный оксид железа. Суммарная реакция может быть представлена следующим уравнением:
Fe + 302 + 2H20 = 2Fe203·H20
(Сталь) + (Кислород) + (Вода) = Гидратированный оксид железа (Ржавчина)
Отсюда также видно, что процесс коррозии протекает в присутствии активаторов – кислорода воздуха и воды. В их отсутствие процесс коррозии не протекает.
Таким образом, по истечении некоторого времени, и с накоплением продуктов коррозионного процесса, коррозия стали становится явной и усиливается. В результате появляются все новые и новые очаги коррозии (формируются новые анодные участки). Поэтому через длительный период времени потеря металла начинает протекать равномерно по всей поверхности, и такая коррозия называется «общей коррозией». Схематично механизм коррозии представлен на рис.1
Рис. 1. Схема коррозионных процессов на стали.
2. Коррозия железобетонных конструкций
3. Влияние на скорость коррозии
Основными факторами, определяющими скорость коррозии стали в атмосфере являются:
- Время насыщения влагой. Это общее время, в течение которого поверхность металлических конструкций находится во влажном состоянии из-за дождя, конденсата и проч. Это означает, что для конструкций находящихся в условиях сухой атмосферы, скорость коррозии будет минимальна, из-за отсутствия воздействия влаги.
- Атмосферные загрязнения. Здесь важно какой тип загрязнения и в каких количествах присутствует в атмосфере (например, сульфаты, хлориды и др.)
- Сульфаты. Данный тип загрязнений появляется из-за сернистого газа (SO2), который является продуктом сгорания топлив. Сернистый газ реагирует с водой или влагой в атмосфере, образуя серную и сернистую кислоты. Промышленность является одним из основных поставщиков сернистого газа.
- Хлориды. Данные загрязнения присутствует в большом количестве в морской атмосфере. Часто даже в радиусе нескольких километров от береговой линии наблюдается высокая концентрация хлоридов в атмосфере.
Хлориды и сульфаты увеличивают скорость коррозии. они реагируют со стальной поверхностью конструкций транспортных сооружений и образуются соответствующие растворимые соли железа, которые концентрируются в питтингах и вызывают «питтинговую коррозию».
Кроме воздействия локальной атмосферы, загрязнения могут быть вызваны, иногда в значительной степени, из-за господствующих ветров. В связи с этим, для практического определения скорости коррозии, необходимо устанавливать как формируется микроклимат вокруг конкретного транспортного сооружения (мосты, путепроводы, барьерные ограждения).
Из-за постоянных изменений в атмосфере, не возможно точно установить (предопределить) скорость коррозии объектов и вывести единый стандарт по определению скорости. Однако климатические зоны классифицируются согласно ISO 12944. Часть 2, а скорости коррозии могут быть определены по соответствующим показателям. Более подробная информация приведена в ИСО 12944 и ИСО 9223.
4. Влияние конструкторских решений на коррозию. Рациональное проектирование
При рассмотрении вопросов коррозии в транспортном строительстве, прежде всего, необходимо обратиться к вопросам проектирования транспортных сооружений (мостовых металлических и железобетонных конструкций, барьерных ограждений). Ведь именно на данном этапе можно устранить до 70-80% коррозионно-активных мест в конструкциях и сооружениях. Старые мосты были спроектированы с большим количеством мелких конструкционных деталей и соединений, таких как связи и заклепки, что сильно затрудняло защитные (антикоррозионные) работы, по сравнению с уровнем современного проектирования данных узлов.
Соединительные элементы мостов, ограждений часто являются источниками коррозионных проблем, т.к. в местах соединений часто возникают потеки продуктов коррозии. В идеальном случае, избежать соединительных элементов можно было бы использовав протяженные (цельные) конструкции. Однако, на практике, избежать соединительных узлов не удается, и здесь можно рекомендовать удалять соединительные элементы от концов балок (ферм) с организацией системы слива накапливающегося в данных местах конденсата.
Также необходимо обращать внимание на производство подготовительных работ, чтобы все элементы конструкций были тщательно очищены (согласно утвержденной документации), во избежание появления коррозионных поражений уже в начальный период эксплуатации металлических или железобетонных конструкций. Кроме этого, необходимо устанавливать на будущие периоды плановые инспекционные работы по обследованию состояния защитного покрытия конструкций и сооружений. Специалисты инжинирингового центра ООО «ПРОМАТЕХ» имеют большой опыт в проведении инспекционных работ на объектах мостостроения. Подробнее в разделе «Сервис-центр».
Доступность конструкций для нанесения защитных покрытий и проведения плановых ремонтных антикоррозионных работ.
Доступ ко всем элементам конструкций позволяет не только производить тщательную очистку поверхности перед нанесением покрытий, но и производить плановые ремонтные антикоррозионные работы. Узкие отверстия, сложные для доступа углы, и труднодоступные поверхности необходимо максимально избегать при проектировании. Другими словами, расстояние между элементами в местах соединения конструкций, и значение угла между элементами жесткости должны обеспечивать полный доступ для нанесения покрытия и его дальнейшей эксплуатации. На рисунках 2 а) - к) ниже приведены примеры таких проектных решений.
Ребра жесткости.
Типичной деталью элементов жесткости конструкций, которые сложно защищать от коррозии, является ребро жесткости. Несмотря на то, что расстояние для доступа к ребрам значительно, на практике тщательно очистить ребра жесткости абразивоструйным методом не удается.
Устранение конденсата и мусора.
Элементы конструкций, которые потенциально могут задерживать влагу или, где может скапливаться мусор, должны быть по возможности исключены. Вот некоторые типичные решения, которые можно применить для устранения указанных мест:
- Сглаживание (зачистка) сварных швов на горизонтальной поверхности,
- Сокращение поперечного разреза ребер жесткости так, чтобы оно было короче и не доходило до нижней полки балки,
- Избегать использования каналов с выходами по направлению «вверх»,
- Уголки располагать таким образом, чтобы вертикальная полка была выше горизонтальной,
- Избегать использования конструкций «Т» - типа для несущих элементов.
Щели и зазоры.
Щели и зазоры, возникающие при сопряжении элементов конструкции, приводят к накоплению и удержанию влаги. Применение высокопрочного болтового соединения приводит к определенной проблеме коррозии на данном участке, поэтому в некоторых случаях применение сварного соединения является предпочтительным с точки зрения устранения коррозии. Но и при использовании высокопрочных болтов для соединения проблему щелей и зазоров можно решить, уменьшив зазор болтового соединения, используя накладные гибкие металлические пластины. Зазоров, возникающих при соединении пересекающихся элементов, также можно избежать, использовав уплотнение из гибких металлических пластин такой же толщины, как и ребра жесткости несущих конструкций, и используя высокопрочные болты для соединения всех трех элементов.
Дренаж и вентиляция.
При сооружении конструкций необходимо уделять внимание правильному устройству дренажа и вентиляции для стальной поверхности, чтобы поддерживать ее в сухом состоянии, т.е. минимизировать «время насыщения влагой». Необходимо избегать близкого расположения балок и поверхности, по которым происходит движение по мосту, должны быть удалены от стальных поверхностей. Кроме этого, можно использовать при проектировании широкие консоли с соответствующими системами дренажа.
![]() рис. 2а). Предпочтительная обработка сварного шва - шлифование.
|
![]() рис. 2б). Радиус скругления отверстия ребра жесткости 40-50 мм.
|
![]() рис. 2в). Не рекомендуется - отверстие ребреа жесткости под углом 450.
|
![]() рис. 2г). Рекомендуемое расстояние от нижней полки несущей балки до ребра жесткости.
|
![]() рис. 2д). Расположение уголков.
|
рис. 2е). Рекомендуемое соединение для узла. |
рис. 2ж). Рекомендуемые расстояния. |
![]() рис. 2з). План уклонов элементов жесткости.
|
рис. 2и). Рекомендуемое расположение ребер жесткости. |
рис. 2к). Расположение сварных стыков для избежания накапливания конденсата. |
Другие решения по рациональному проектированию можно найти в ИСО 12944, часть 3, а также получить консультацию у специалистов ООО «ПРОМАТЕХ».
Другие публикации
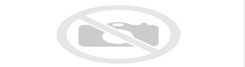
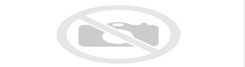